Summary:In the realm of custom low-voltage power cable wires, the choice of insulation type is not merely a matter of enclosing conductors; it profoundly infl
In the realm of custom low-voltage power cable wires, the choice of insulation type is not merely a matter of enclosing conductors; it profoundly influences both performance and longevity across various operational environments and conditions. Understanding the impact of insulation materials on these critical aspects is essential for engineers and decision-makers tasked with selecting the optimal cable solution for specific applications.
Electrical Performance
Dielectric Strength: One of the primary functions of insulation is to provide a barrier between conductors, preventing electrical current leakage. Insulation materials with high dielectric strength, such as cross-linked polyethylene (XLPE) or polyvinyl chloride (PVC), excel in maintaining electrical integrity even under high voltages. This property ensures stable performance and reduces the risk of electrical breakdown over time.
Insulation Resistance: Different insulation materials offer varying levels of insulation resistance, crucial for maintaining signal fidelity and preventing leakage currents. Materials like fluoropolymers (e.g., PTFE) exhibit excellent insulation resistance, ideal for applications requiring precise signal transmission and minimal signal loss.
Mechanical Performance
Flexibility: In applications where cables undergo frequent bending or flexing, the flexibility of insulation materials becomes critical. Silicone rubber and elastomeric materials provide superior flexibility, reducing stress on conductors and extending the cable's operational life in dynamic environments.
Abrasion Resistance: Cables subjected to mechanical wear from friction or contact with abrasive surfaces benefit from insulation materials with high abrasion resistance. Thermoplastic polyurethane (TPU) and polyethylene terephthalate (PET) offer robust protection against abrasion, ensuring longevity even in harsh industrial settings.
Tensile Strength: The ability of insulation to withstand pulling forces without tearing is essential for cables installed over long distances or in applications requiring tension resistance. Materials like polypropylene and nylon exhibit high tensile strength, maintaining structural integrity under mechanical strain.
Thermal Performance
Temperature Rating: Insulation materials must withstand operational temperatures without degrading or compromising safety. Thermoset materials such as ethylene propylene rubber (EPR) or XLPE are known for their high temperature ratings, ensuring reliability in both high and low-temperature environments.
Heat Resistance: Some applications demand insulation materials capable of withstanding extreme heat conditions. Silicone rubber excels in high-temperature environments, maintaining electrical and mechanical properties under prolonged exposure to heat.
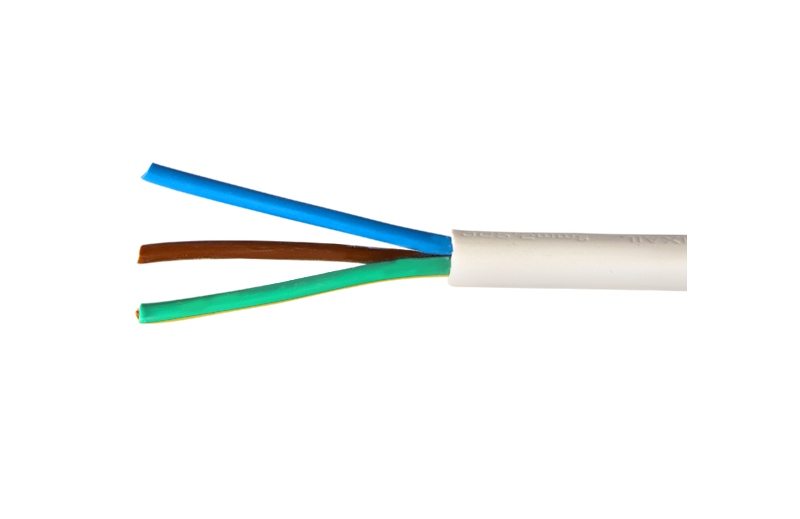
Longevity
Environmental Resistance: Cables deployed in diverse environments encounter varying levels of moisture, chemicals, and UV radiation, all of which can degrade insulation over time. Materials like PVC and fluoropolymers offer excellent resistance to moisture and chemicals, enhancing longevity in harsh conditions.
UV Resistance: Outdoor applications expose cables to UV radiation, which can accelerate degradation and compromise performance. UV-resistant materials like polyethylene and cross-linked polyethylene (XLPE) mitigate the effects of sunlight exposure, prolonging the cable's service life.
Ageing Characteristics: Insulation materials age differently based on their chemical composition and exposure conditions. Stable materials like PVC and XLPE are designed to resist degradation over extended periods, maintaining consistent performance throughout the cable's lifecycle.
Mechanical Durability: The durability of insulation materials impacts the overall robustness of the cable assembly. Materials with inherent mechanical strength, such as TPU and fluoropolymers, ensure cables remain resilient against mechanical stresses, including vibration and impact.