Summary:Conductor Materials: The Heart of ConductivityThe foundation of every Cat6 patch cord cable begins with its conductors. Traditional Cat6 cables often
Conductor Materials: The Heart of Conductivity
The foundation of every Cat6 patch cord cable begins with its conductors. Traditional Cat6 cables often use bare copper for its superior conductivity, ensuring minimal signal loss even over longer runs. However, cost-conscious manufacturers sometimes opt for copper-clad aluminum (CCA) as a cheaper alternative. While CCA saves upfront costs, it sacrifices longevity and performance at high frequencies. Over time, aluminum oxidizes, leading to degraded conductivity—a critical flaw for environments demanding consistent 10 Gbps speeds.
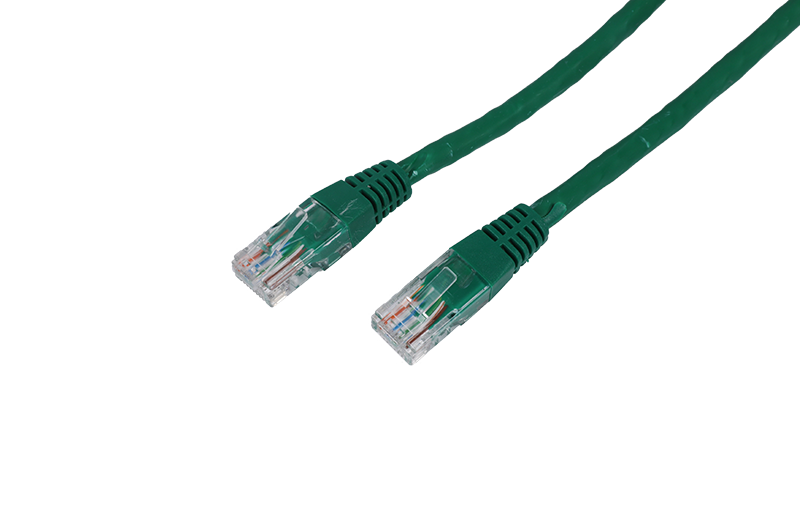
Advanced manufacturers are now experimenting with hybrid conductors, combining thin copper layers over aluminum cores to balance cost and performance. This innovation ensures Cat6 patch cord cables remain both cost-effective and reliable, even in demanding industrial or data center setups.
Dielectric Insulation: The Silent Signal Guardian
Beyond conductors, the dielectric insulation plays a starring role in reducing crosstalk and attenuation. Traditional polyethylene insulation has served Cat6 cables well, but emerging materials like fluoropolymers (e.g., PTFE) are pushing boundaries. These materials boast lower dielectric constants, minimizing signal interference and enabling higher-frequency transmissions.
Fluoropolymers also excel in extreme temperatures, maintaining their integrity in environments ranging from freezing server rooms to hot industrial floors. This makes them a game-changer for Cat6 patch cords deployed in harsh settings, where conventional insulation might degrade. Engineers are now pairing these materials with ultra-tight wire twisting to amplify noise reduction, ensuring that data integrity stays intact even in crowded cable bundles.
Jacketing Compounds: The Armor Against the Elements
The outer jacket isn’t just a protective shell—it’s a battleground against environmental hazards. Cat6 patch cord cables designed for commercial or industrial use often feature flame-retardant jackets made of low-smoke zero-halogen (LSZH) polymers. Unlike traditional PVC jackets, LSZH materials minimize toxic fumes during combustion, complying with strict safety standards in plenum spaces (e.g., office ceilings).
For outdoor or marine applications, manufacturers are turning to UV-resistant and water-blocking jacketing compounds. These blends protect against UV degradation, moisture ingress, and physical abrasion, extending the lifespan of Cat6 patch cords in rugged outdoor deployments. Meanwhile, flexible PVC options remain popular for indoor use, offering a balance of durability and bend tolerance.
The Future of Cat6: Materials Driving Innovation
As networks evolve, so do the materials shaping Cat6 patch cord cables . Researchers are exploring self-healing polymers for jackets and graphene-enhanced conductors to further reduce latency. These advancements promise cables that adapt to damage, resist corrosion, and deliver blistering speeds—even in extreme conditions.
For professionals, understanding these material nuances isn’t just about staying ahead of trends—it’s about future-proofing infrastructure. Whether you’re wiring a data center or retrofitting a smart factory, the right materials mean the difference between a functional network and a flawless, resilient one.